Yango Tech expands partnership with ROOTS with Yango Tech Retail to accelerate AI-powered retail vision in the UAE
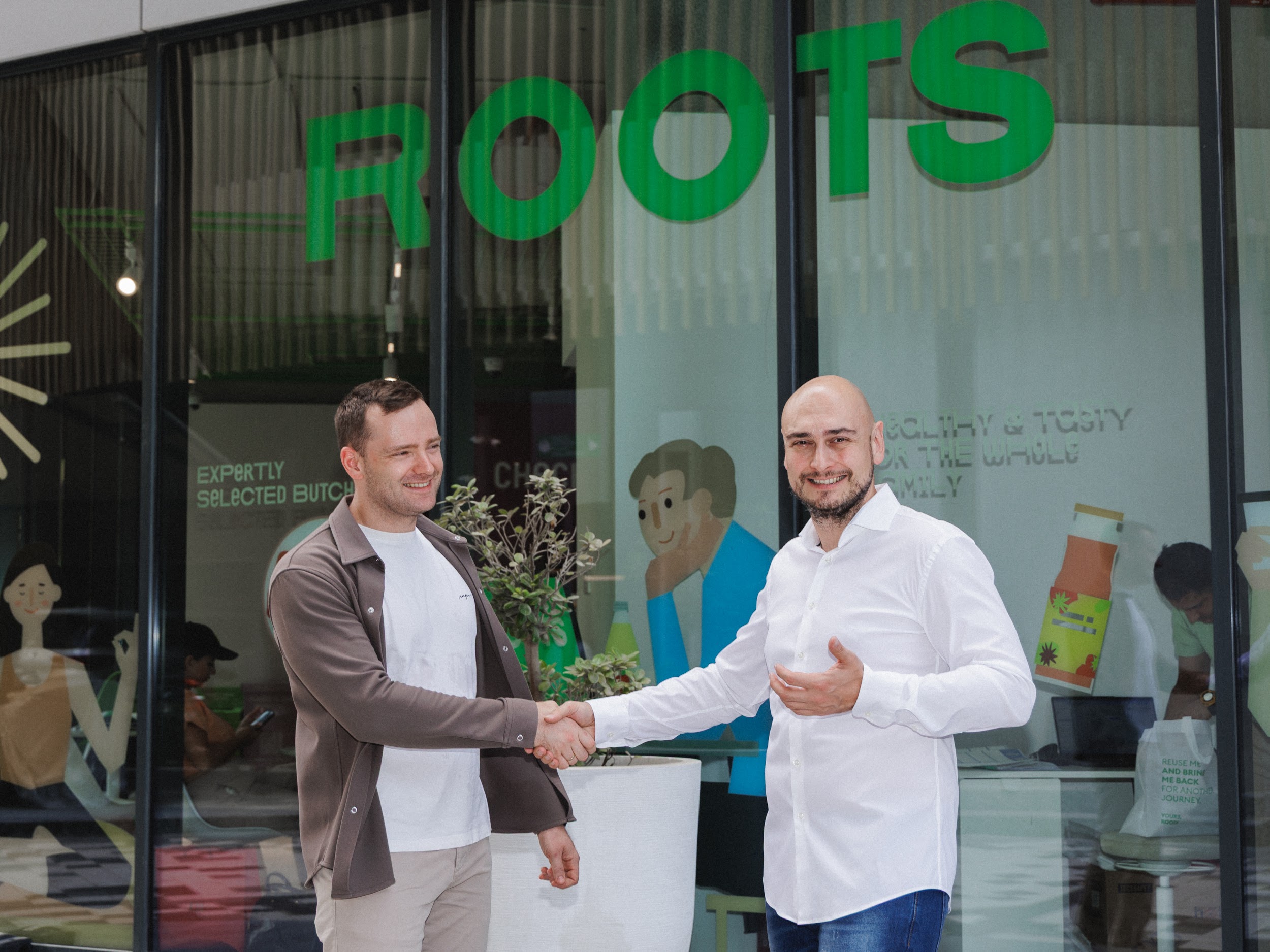
Tracking warehouse inventory and ensuring optimal On-the-Shelf Availability (OSA) stock levels is crucial for business operations. With accurate management of inventory and stock levels, companies can reduce costs associated with both.
By leveraging a warehouse management system powered by smart algorithms and software, businesses gain real-time visibility into their inventory, empowering them to make data-driven decisions. This ensures that products are readily available for customers when they need them, fostering customer loyalty and providing a competitive edge in the market.
The main challenge when tracking inventory in a warehouse is stock accuracy and real-time visibility.
This involves effectively managing and updating inventory data as stock moves in and out of the warehouse. Factors such as manual errors, delayed or inconsistent data entry, misplacement of items, and inadequate inventory management systems can result in discrepancies between recorded and actual inventory levels. This lack of visibility can lead to the above-mentioned stockouts, overstocks, inefficient order fulfillment, and reduced customer satisfaction.
Overcoming this challenge requires implementing a stable and reliable system that consists of: inventory tracking systems, scanning technologies like barcoding or RFID, and established standardized processes. Once optimized regular inventory audits are required to maintain accurate and up-to-date inventory information in the warehouse.
The main challenge when tracking inventory in a warehouse is the accuracy and real-time visibility of stock. This involves effectively managing and updating inventory data as stock moves in and out of the warehouse.
Common factors are:
A streamlined warehouse is the heart of successful e-commerce. A consistent history of orders made in full is created with the help of technology powered up by advanced custom assets. Yango Tech developed a solution that tackles the mentioned issues affecting warehouse inventory and therefore stock levels and missing items.
The key components of the solution implemented by Yango Tech are as follows:
The implementation of the Warehouse Management System and supporting solutions yielded the following results:
To successfully optimize warehouse operations, Yango Tech implements a custom tech stack comprising the Warehouse Management System and Picker App. This solution provides accurate, timely information, ensuring optimal OSA levels and with consistent availability improves customer satisfaction. Real-time inventory tracking, efficient order collection, and data-driven decision-making contribute to the growth and profitability of successful e-commerce.